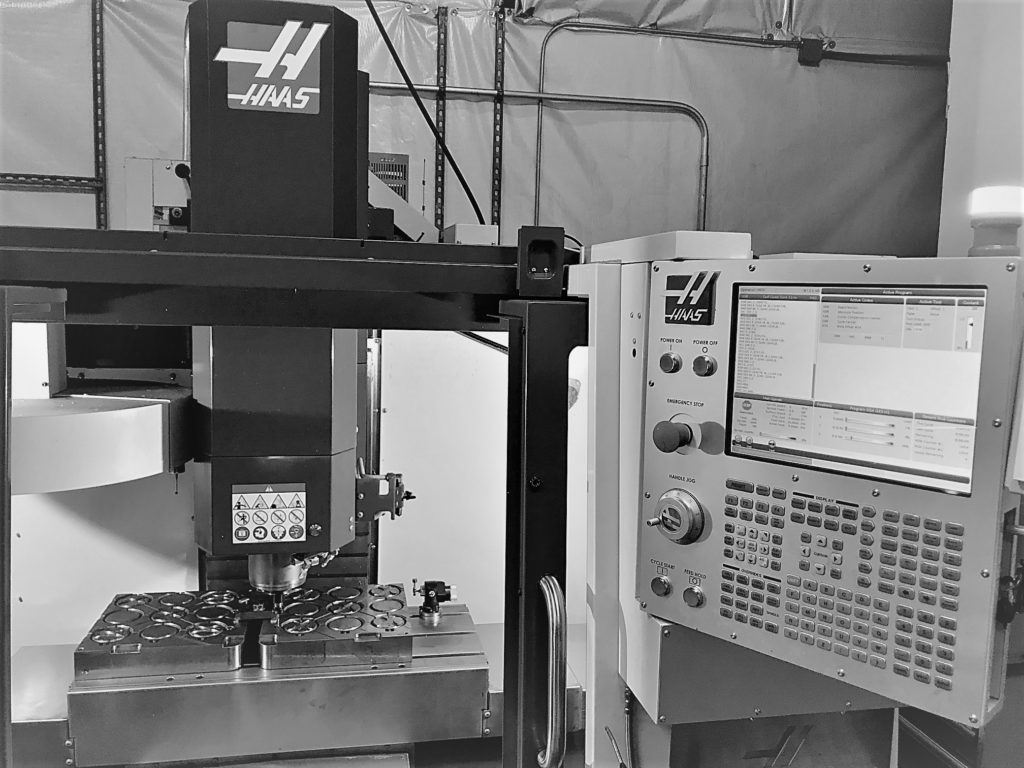
Mold Makers and Tool and Die Craftsmen – Mold making is a skill that requires a high mechanical and technical aptitude coupled with years of experience in metal working, fitting and trouble shooting. Mold makers are a critical partner to Injection Mold process technicians in troubleshooting and maximizing production efficiencies. We have a great team and would like to build more tools in the U.S.A., but are limited by our ability to attract qualified and experienced mold makers. As such, we are always on the look for experienced mold makers to join our team. If you are an experienced tool and die or mold maker, we would welcome the opportunity to talk to you about joining our team.
Texas Injection Molding designs and manufactures injection molds both in-house in Houston, Texas and with long-term offshore partners.
Injection Mold Builders
We have experience in building all SPI Class tools including tools with hand loaded cores and inserts, multiple slides, automatic unscrewing cores, hot runner systems and tools for over-molding.
Prototype Injection Molds – SPI Class 104 & 105 molds. Prototype molds are often used to develop proof of concept or initial product launch. To provide reduced lead-times and lower cost, Texas Injection Molding utilizes our own Master Unit Dies and manufactures custom cores and cavities in pre machined insert blocks. Prototype injection molds are designed to run low volume, but with quality steel can product high volume. Prototype injection molds are typically single cavity and may not be cost-effective for high volume production. For parts with complex geometry and undercuts, hand loaded inserts can be utilized to create these features without cost of slides and automatic unscrewing cores.
Production Injection Molds – SPI Class 102 & 103 molds. These injection molds account for the majority of the molds built by Texas Injection molding and are designed to product up to one million cycles. Part volume and geometry will drive number of cavities, runner style, slides, lifters, collapsible cores and automatic unscrewing cores.
High Volume Injection Molds – Class 101 molds are designed for very high production volumes and are typically highly automated. All high volume injection molds will have hardened molding surfaces, wear plates and will have special attention to runner systems and cooling systems. Often these tools are designed to be used with automation outside of the mold and involve consideration for end-of-arm tooling to place or remove parts via robot. Visual inspection systems may also be added to automate and document inspection during production. Inspection systems can be tied into machine controls to stop production or issue alarms if a particular specification is out of tolerance.
Injection Mold Design
Every mold design goes through a 3 stage Mold Design Review:
- Preliminary Mold Design Review – This review ensures that we have all the final customer specifications, 3D drawings, reviews basic mold specifications and verifies identified molding machine(s) sizes quoted prior to sending to tool shop for Tool Design. Preliminary review is reviewed and signed off by Project Engineer, Tooling Engineer and Process Engineering. Preliminary Mold Design review
- Mold Design Review – Following completion of initial injection mold design, detailed 2D and 3D mold drawings and specifications are reviewed. The mold design checklist ensures that all the major components of the mold design are considered and reviewed. These include fit to molding machine, Mold Base, Cores and Cavities, Ejection system, Cooling and Runner system. Mold Design Review
- Mold Review – All in-house and offshore molds go through a final inspection checklist prior to release to production for FAI trial runs. Mold Review Checklist
In-House Tooling Capabilities
- Mold design Review – All molds built in-house or off-shore go through a complete mold design review
- New mold pilot production support – Upon receipt of transfer tooling or off-shore tooling, the Texas Injection Molding tool shop will complete incoming inspections and work with Process Engineering to do any final fitting, modifications or tuning to provide optimum performance.
- Engineering Change Requests – For existing tools that require modifications to dimensions or features, Texas Injection Molding has in-house capabilities to make most modifications.
- Routine Maintenance – At the completion of all production runs, molds are inspected and tagged for any issues that need to be addressed prior to next production run. Between run maintenance of lubrication, protective spray and blowing out of cooling channels is performed. Texas Injection Molding operates an ERP system that captures the number of cycles for each tool. A preventative maintenance schedule is prescribed for each specific mold. At the appointed number of cycles molds are inspected, cleaned and lubricated. Cooling systems and hot runner systems are also inspected and tested.
- Texas Injection Molding maintains limited capacity to build SPI class 103, 104 and 105 molds in-house.
- End-of-arm tooling for robots, cooling fixtures and assembly fixtures are designed and built in-house.